July, half journey of 2025 has come to an end. The woodworking machinery industry is constantly changing.
Nowadays, the woodworking machinery industry is at a critical stage of intelligent transformation. In 2025, the industry will present a three-level development pattern of “intelligent high-end competition, flexible mid-range market, and green low-end production capacity”.
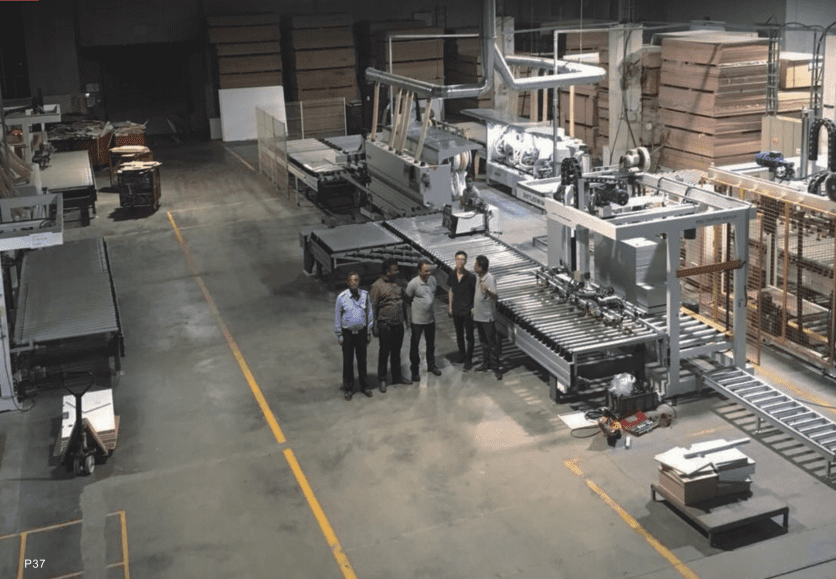
Driven by the explosion of customized furniture and the industrialization of construction, a group of iconic devices are reshaping the production mode of wood processing by integrating the Internet of Things, AI algorithms, and precision manufacturing technology.
These devices not only meet the flexible production needs of small batches and multiple varieties, but also achieve breakthroughs in precision, efficiency, and environmental performance, becoming the core carrier for China’s woodworking machinery to catch up with international leading levels.
CNC Nesting Center: the hub of flexible customized production
As the core equipment for the production of panel furniture, the CNC nesting centers have evolved from simple cutting equipment to comprehensive processing platforms that integrate optimized design, automatic warehousing, and intelligent execution. Its technological breakthroughs are mainly reflected in three aspects:
- Intelligent optimization algorithm: By integrating CAD/CAM software, the cutting scheme with the highest material utilization rate is automatically generated, which increases the material yield by more than 10% compared to traditional electronic saws.
- Automatic silo integration: Combining warehouse management software and automatic feeding system, achieve full process automation from material retrieval, feeding to material opening, reducing manual intervention by 50%.
- Real time monitoring system: equipped with tool wear sensors and vibration monitoring modules, reducing unplanned downtime through AI predictive maintenance, and improving overall equipment efficiency (OEE) by over 25%.
Fully automatic six side drilling machine: a precision revolution for customized furniture
In the field of customized furniture, traditional drill bits are being quickly replaced by fully automatic six side drilling machine due to the need for manual replacement of drill bits and low positioning accuracy. The core advantages of this device are:
- Six sided synchronous processing: By using a three-dimensional drilling layout, all hole positions of the board can be processed in one clamping, eliminating multiple positioning errors.
- Barcode automatic recognition: After scanning the board information, the processing program is automatically called, and switching orders only takes 5 seconds, suitable for small batch production.
- Precision breakthrough: Using linear motor drive and visual compensation system, the drilling position error is controlled within ± 0.05mm, which is better than the international standard of ± 0.1mm.
According to market data in 2025, the penetration rate of fully automatic six sided drills in customized furniture enterprises has reached 65%.
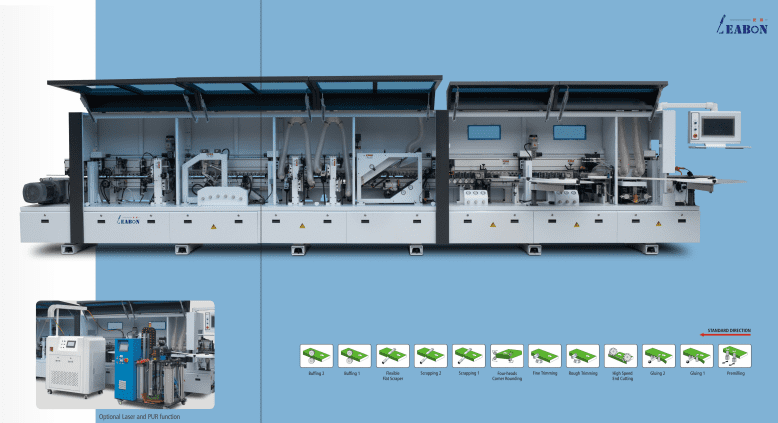
High end edge banding equipment: breakthrough in magnetic levitation technology
The quality of edge banding directly affects the aesthetics and durability of furniture, while traditional edge banding machines have problems such as uneven glue lines and obvious seams during high-speed operation. The new generation of magnetic levitation edge banding machine solves industry pain points through two major innovations:
- Ultra high speed processing: The magnetic levitation high-speed flexible edge banding machine launched by Hongya CNC adopts linear motor direct drive technology, with a processing speed of 42 meters per minute, close to the level of German Haomai laser edge banding machines, breaking the import monopoly.
- Glue line control: Through precise temperature control (± 1 ℃) and pressure adaptive system, the glue seam is achieved to be ≤ 0.1mm, overcoming the long-standing problem of “fine gaps” in domestic equipment.
Challenges and Future Paths
Despite significant progress in mainstream equipment, the industry still faces challenges of relying on imported core components (with high-end CNC systems accounting for 65% of imports) and difficulties in transforming small and medium-sized enterprises (with intelligent transformation costs exceeding 10 million yuan)
The next phase of China’s woodworking machinery will undoubtedly engage in more intense competition in the construction of intelligent ecology and deep integration of craftsmanship.